What does Magic Johnson and a twenty foot robot have in common? You guessed it, Automate 2017. While this might seem like an odd pairing, it accurately reflects the current state of the robotics industry. Already 2017 is on pace to beat last year’s $19 billion investment record, with the recent announcements of Intel’s $15B purchase of Mobileye; ABB’s $2B acquisition of Bernecker & Rainer; and Ford’s $1B investment in Argo AI.
The excitement inside Chicago’s McCormick Center on Wednesday was palpable, as Automate 2017 brought together not just established industrial leaders but also innovative startups at The Launchpad Competition. Eight mechatronic entrepreneurs competed to impress the judges (Chris Moehle of The Robotics Hub, Steve Taub of GE Ventures, Melonee Wise of Fetch Robotics, and yours truly) in the hopes of winning a $10,000 prize from GE. Andra Keay of Silicon Valley Robotics, the afternoon’s Master of Ceremonies, kicked off the event by reminding the audience that some of the past participants have gone on to change the robotic landscape and raised tens of millions of dollars from investors. As we peek into the robotic crystal ball, please meet this year’s contestants:
Andros Robotics: Teaching humans to walk again with robots
Maciej Pietrusinski, CEO of Andros Robotics, shared with the audience the history of his invention (force-controlled actuators) which began as a PhD thesis on “The Robotic Gait Rehabilitation Trainer” in Northeastern University’s Biomedical Mechatronics Laboratory. The goal of Andros is to build low-cost service robots for the medical rehabilitation market. To achieve this objective the company is selling its proprietary force feedback actuators to academic labs and other robot companies. In the future, Andros plans to market an end-to-end exoskeleton solution. To date, Andros has yet to receive funding from SBIR grants from the National Science Foundation.
In his IEEE paper, Pietrusinski stated in 2014 that this invention will increase the “life expectancy” of the world’s growing geriatric population by maintaining their quality of life through “independent gait.” Among the disabilities targeted is stroke-caused hemiplegia. There are approximately 6.5 million stroke survivors and about 800,000 new cases every year in the USA. Through therapeutic robotic exoskeleton-walkers, Andros is improving the quality of life of the world’s largest demographic group. As a fan of exoskeletons, I want to encourage Andros to focus on raising capital from social impact investors that could assist Pietrusinski’s team to achieve greater success in its ambitious goal.
Appelix: Replacing jobs with drones
There are some jobs that are just too dangerous for humans, painting bridges is one of them. Meet Appelix – a drone manufacturer and painting services company which has developed a novel approach to automating large-spray operations. Their solution: a tethered drone platform that connects to a 3,000 PSI air compressor and power supply to continuously spray paint large structures: from bridges to commercial ships to gas storage tanks. The industrial-grade drone system is built entirely by the company and rented out on a job-by-job basis. It has already completed a number of successful pilots.
“We’ve taken people out of the dangerous situations and replaced them with automated robotics,” said Bob Dahlstrom, founder of Appelix. “Never mind the cost efficiencies.” According to Dahlstrom, the current product is market ready to begin widescale operations. In the future, Appelix will seek to expand its services business to include window washing, infrastructure inspections, and possibly de-icing planes. Appelix’s patent-pending “Worker Bee Drone” could even take over New York City’s “Façade Inspection Safety Program” that is still done by hand with humans hanging from ropes holding pickaxes hundreds of feet above walking pedestrians.
Augmented pixels: Cost-effective computer vision for robots
One of the most impressive elements of the Automate 2017 Conference was the number of computer vision and photonic companies in the marketplace. A key element in autonomous anything, from vehicles to robots, is vision. However, the spectrum of vision has many complex variables including optical materials, detector ranges and laser line of site. Together these elements make up a variety of sensors (LIDAR, cameras, radar, etc). The best applications of photonics are a targeted specific problem, like obstacle detection, versus deploying a sensor for robotic everything.
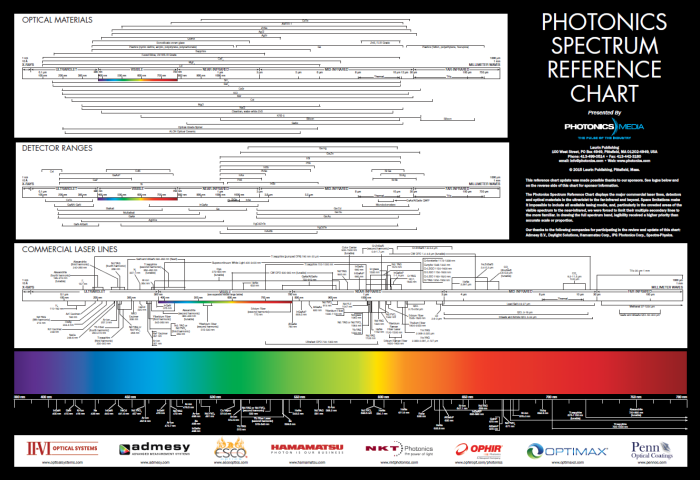
Augmented Pixels is utilizing camera sensors for Simultaneous Localization And Mapping (SLAM) solutions for low-compute powered devices like drones. The company plans to evolve their solution into a true autonomous navigation platform for drones and robots in GPS-denied environments. In addition, the startup is also working on a hardware-optimized solution for indoor navigation with mobile phones and AR/VR glasses similar to Google’s Project Tango initiative.
Vitaliy Goncharuk, founder and CEO of Augmented Pixels, explained his market opportunity, “It became clear that the leaders of all markets from the automotive industry to drone and household robots understood that the future belongs to companies that can simplify the use of its gadgets to the level of an app for the smartphone. This requires a fundamentally new way of thinking about the design of future systems and user interfaces. Our company’s technology and the platform play key roles in this technology stack.” Melonee Wise asked Goncharuk how he will be able to compete now that Project Tango is open sourced (the question remained unanswered).
HEBI Robotics: Providing dexterity for robot systems
For a long time, deploying automation around a factory meant redesigning a production line around a robot’s reach. HEBI Robotics aims to change this dynamic through the deployment of modular elastic actuators. The HEBI modules enable the ability to create custom robots of virtually any configuration; from wheeled to collaborative arms with multi-degrees of freedom. As shown below, it can even feed you pasta:
Based in Pittsburgh PA, the HEBI technology is the result of years of research at the Biorobotics Lab at Carnegie Mellon University. According to the founder Bob Raida, “HEBI develops Lego-like robotic building blocks that enable rapid development and deployment of custom collaborative robots. Our customers are academia, R&D organizations and industrial end users that have a need for robots that can be designed and deployed quickly, then re-used as needs change. HEBI offers several families of modular actuators that function as full-featured robotic components as opposed to simple servo motors.” Last year at RoboBusiness, Modbot impressed many with the concept of a modular robotic arm, HEBI is now (cost-effectively) fulfilling on that promise.
Kinema systems: Automating the warehouse one box at a time
According to his blog post, Sachin Chitta, CEO of Kinema Systems, says “Kinema Pick is the first in a series of solutions from Kinema Systems for the ‘holy grail’ of industrial robotics – random picking.” Chitta’s robotic systems utilizes an off-the-shelf (Yaskawa) robotic arm with a suite of proprietary vision sensors, deep learning algorithms, and motion-planning software to solve the most critical problem in the warehouse – moving pallets. Every e-commerce company is following Amazon’s lead in automating distribution centers and operations. The problem to date has been the unstructured environment of random placements of pallet boxes on a moving conveyor belt. According to the pitch, Kinema’s self-learning systems now offers for the first time a turn-key configurable solution for its customers and their unskilled laborforce.
Chitta, a former Willow Garage Alum, explains “the biggest differentiator we bring to the table, is dealing with these situations [unstructured environments] where there is lack of structure or there is variety, so that we can address the actual problems facing logistics, warehouses, shipping, and even in manufacturing as well.” Chitta is definitely someone to watch in 2017.
Robotic materials: Grippers that understand touch
One of the biggest challenges in the robotic industry is understanding touch and tactile sensing. Robotic Materials claims to have “developed patent-pending sensors and control systems to be the first and only effective tactile sensing solution for collaborative robot applications.” Their secret sauce, developed at the University of Colorado, is a combination of proximity, contact, and force sensing that enables robots to accurately identify, grasp, and manipulate previously unknown parts, from ballpoint pens to water bottles to steel rims. The key to their solution is everything is integrated on the device, without the need for reprogramming, cloud hosting or learning-based system.
According to CEO Scott Thomas, “we are currently selling grippers and fingers for a select and growing number of robots and prosthetic devices (Rethink Robotics, Kinova, Bebionic), but wish to move up in the value chain to become a solution provider for robotic manipulation in unstructured environments to industry, startups and hobbyists.” I wonder how soon will Scott get a call from ABB or Kuka?
SAKE robotics: The ultimate inexpensive gripper
A key factor in the growth of collaborative and humanoid robots will be the capabilities to do useful tasks cost-effectively in chaotic environments. SAKE Robotics aims to be a game changer with their low-cost grippers that utilize tendons as the primary link between actuators and finger-like motion. While many other grippers on the market utilize tendons, there has been a serious reliability issue due to strength & wear. SAKE’s patent pending “Ceramic Tendon Technology” provides a high strength, low wear, low resistance and low-cost solution.
Their EZGripper Dual robotic grippers have been shown to reliably pick up and hold a variety of objects weighing between grams and multiple kilograms (from pencils to large objects). In addition, EXGripper enables 360 degree rotation with the grasp center aligned to the axis of rotation. According to Paul Ekas, founder of SAKE, “our vision to deliver the lowest cost, high dexterity robotic grippers [hands] that enable next generation, high value robots.” As Paul presented, I wondered how soon will Pepper be sporting ExGrippers.
Vention – Web-based industrial machine builder engine
Working on a factory floor often requires creativity in designing new processes and support machines to meet market demands. As manufacturing becomes more mechanized, Vention plans on enabling corporate managers with the ability to build and order machines via a web-browser in just a few days. According to the pitch, their platform is an “AI-enabled” cloud CAD application that integrates an ever-growing library of industrial “Lego-style” modules. This means that regardless of the design, structural, motion, and control parts are fully compatible with one another, saving time and money.
Etienne Lacroix, CEO, explained that “it became obvious to us that the next frontier for faster machine design wasn’t better design tools or higher performance hardware, but rather the integration between the two.” Lacroix’s partner and company CTO, Max Windisch, further states that “with the help of artificial intelligence, we are paving the way for significant democratization of mechanical engineering. We want to enable design-savvy individuals who never used a CAD software, to 3D design industrial machines and prototypes. Similar technology democratization in web development (i.e., WordPress, Squarespace, Wix) were complete game-changers; we are creating the equivalent for machine design.” A web-based machine platform is very compelling, however, inventory management could be the reason why no one has done this to date.
Just like Magic Johnson, the robot industry is on the path to another championship season with this team of innovators.
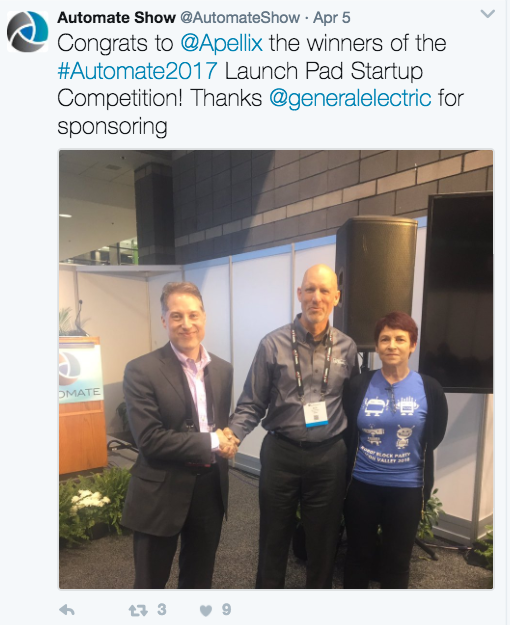
tags:
Automate 2017,
Business Deal,
c-Events,
cx-Business-Finance,
cx-Research-Innovation,
Event,
Robotics technology
Oliver Mitchell
is the Founding Partner of Autonomy Ventures a New York based venture capital firm focused on seed stage investments in robotics
Oliver Mitchell
is the Founding Partner of Autonomy Ventures a New York based venture capital firm focused on seed stage investments in robotics